📐 "First 50 Enterprise Queries Get Custom 3D Warehouse Design" Plan
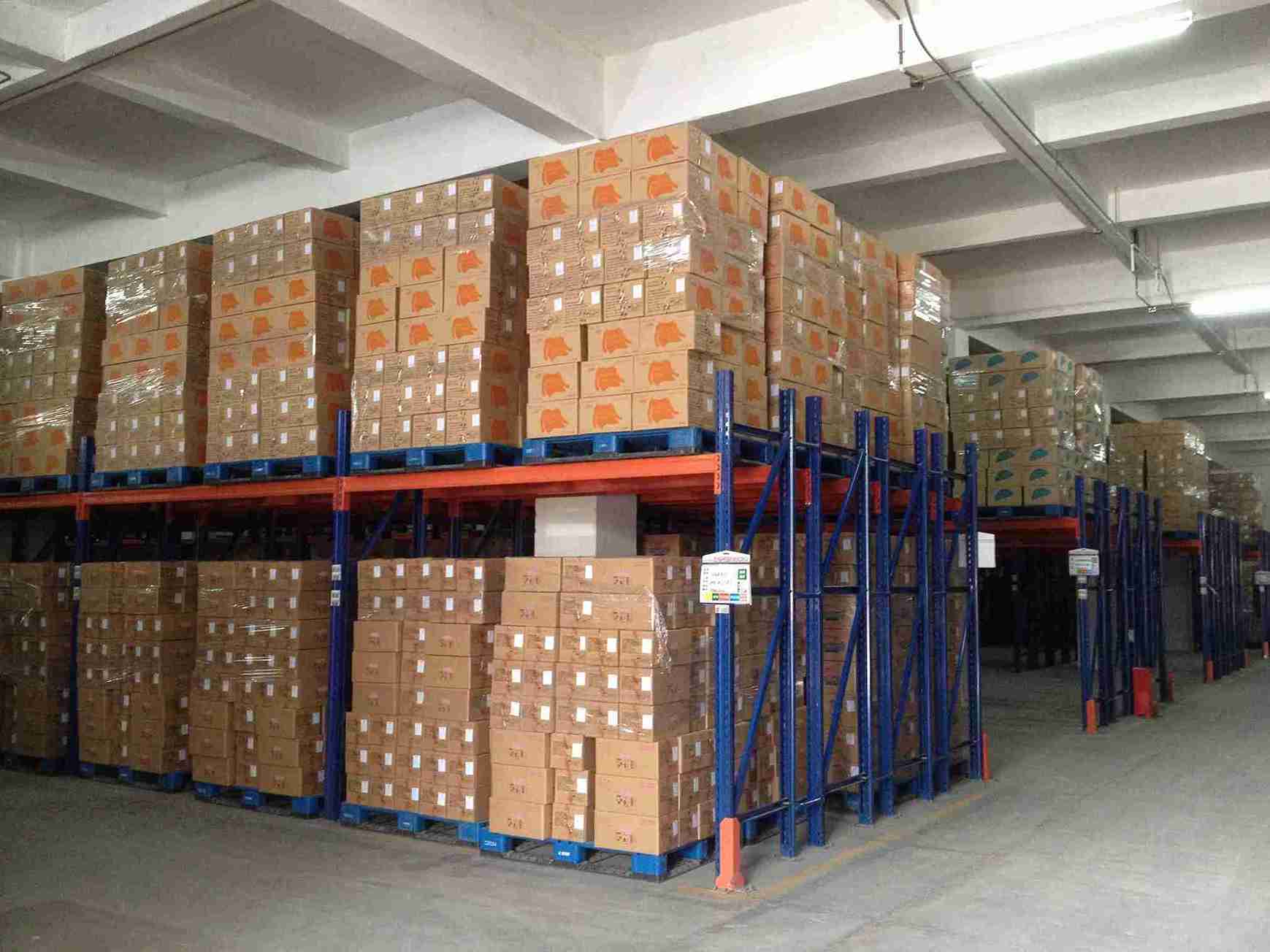
Introduction: The Power of High-Density Storage in Modern Warehousing
In today’s fast-paced logistics environment, maximizing warehouse space while maintaining efficiency is a top priority. High-density storage solutions, particularly double deep racking, have emerged as game-changers for businesses looking to increase storage capacity without sacrificing accessibility. But is this the right fit for your operation?
This comprehensive guide dives deep into high-density storage systems, their benefits, drawbacks, and how they compare to other warehouse solutions. We’ll also provide an ROI calculator to help determine if double deep racking is a cost-effective investment for your facility.
By the end, you’ll have a clear, data-driven understanding of whether high-density pallet storage aligns with your operational needs—and how it can boost efficiency, reduce costs, and future-proof your warehouse.
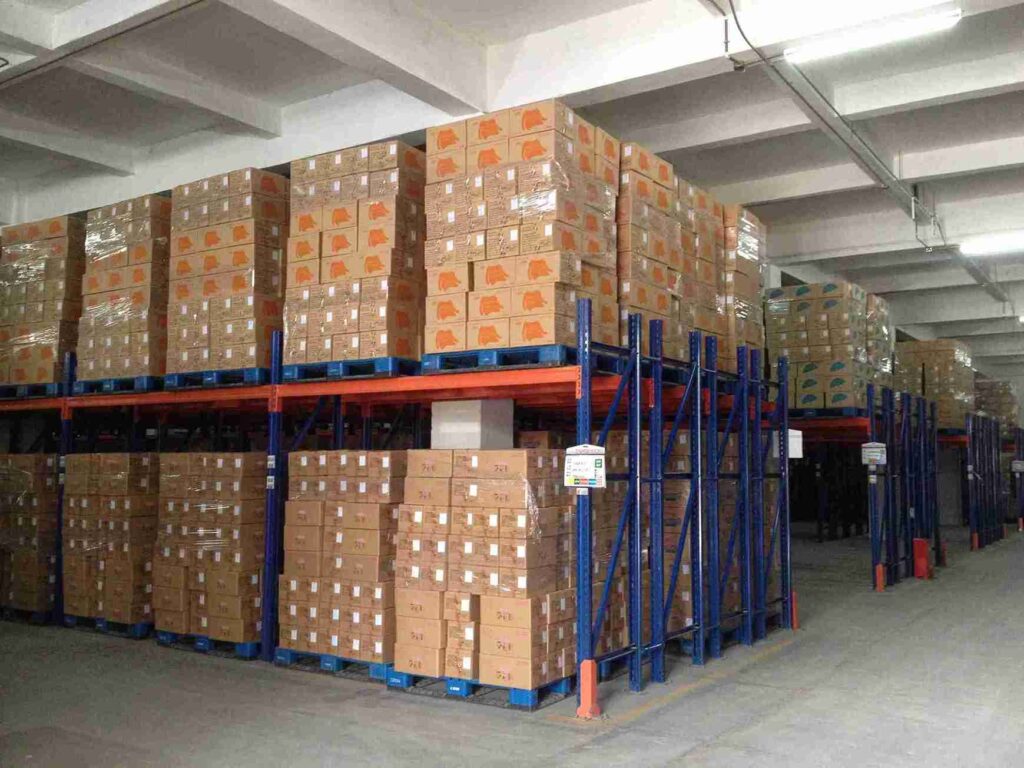
What Is High-Density Double Deep Racking?
High-density storage refers to warehouse systems designed to maximize space utilization by reducing aisle space and increasing vertical or deep storage. Double deep racking, a leading high-density solution, stores pallets two-deep instead of the traditional single-deep arrangement.
How Does High-Density Double Deep Racking Work?
- Uses narrow aisle forklifts (reach trucks) to access the second pallet.
- Requires uniform pallet sizes for smooth operation.
- Best suited for high-volume SKUs with consistent inventory turnover.
Compared to selective racking, high-density double deep setups reduce aisle space by up to 50%, allowing for more pallet positions per square foot.
Key Benefits of High-Density Double Deep Racking
1. Unmatched Storage Density (Up to 50% More Space Utilization)
By eliminating every other aisle, high-density double deep racking nearly doubles storage capacity compared to single-deep systems.
Case Study: A mid-sized e-commerce warehouse increased its pallet positions by 45% after switching to high-density storage, avoiding a costly expansion.
2. Cost-Effective Expansion Without Relocation
Instead of leasing additional warehouse space, businesses can optimize existing layouts with high-density configurations, saving thousands in real estate costs.
3. Improved Inventory Control & Stock Rotation
With FIFO (First-In, First-Out) or LIFO (Last-In, First-Out) options, warehouses can better manage stock rotation—critical for perishable goods or time-sensitive inventory.
4. Enhanced Safety & Structural Stability
- Heavy-duty steel frames ensure durability under high loads.
- Load backstops prevent pallets from shifting, reducing workplace accidents.
5. Faster Order Fulfillment & Reduced Travel Time
Fewer aisles mean shorter travel distances for forklifts, improving order picking speed by up to 20%.
Potential Drawbacks of High-Density Double Deep Racking
While high-density storage offers significant advantages, it’s not perfect for every operation.
1. Limited Accessibility for Rear Pallets
- Second-row pallets require specialized forklifts (reach trucks).
- Not ideal for fast-moving SKUs needing instant access.
2. Higher Forklift Investment
- Standard counterbalance forklifts won’t work.
- Requires narrow aisle (NA) or reach trucks, increasing equipment costs.
3. Reduced Flexibility for Odd-Sized Loads
- Best for uniform pallet sizes.
- Difficult to adjust for oversized or irregular loads.
4. Slightly Slower Retrieval Times for FIFO Systems
If using FIFO, retrieving the second pallet adds minor delays—though this is often offset by space savings.
High-Density Double Deep vs. Other Warehouse Storage Systems
High-Density Double Deep vs. Selective Racking
Feature | Double Deep | Selective Racking |
---|---|---|
Storage Density | High (2-deep) | Low (1-deep) |
Accessibility | Moderate (requires reach trucks) | High (direct access) |
Cost | Moderate (higher forklift investment) | Low (standard forklifts) |
Best For | High-volume, uniform SKUs | Mixed SKUs, frequent access |
High-Density Double Deep vs. Drive-In Racking
- Drive-in racking allows ultra-deep storage (5+ pallets deep) but has slower retrieval times.
- High-density double deep offers a balance between density and accessibility.
High-Density Double Deep vs. Push-Back Racking
- Push-back racking is more dynamic (LIFO-based) but costlier to install.
- Double deep is simpler and more affordable for medium-density needs.
Is High-Density Double Deep Racking Right for Your Warehouse?
Ideal Scenarios for High-Density Storage
✔ High-volume SKUs with consistent pallet sizes.
✔ Limited warehouse space needing maximized storage.
✔ Operations already using reach trucks or narrow aisle forklifts.
When to Avoid High-Density Double Deep Racking
✖ Highly variable pallet sizes.
✖ Extremely fast-moving SKUs requiring instant access.
✖ Budget constraints preventing forklift upgrades.
ROI Calculator: Estimating Cost Savings with High-Density Storage
To determine if high-density double deep racking is financially viable, consider:
- Current Storage Costs (per sq. ft.)
- Projected Space Savings (up to 50%)
- Forklift Upgrade Costs (reach trucks vs. standard forklifts)
- Labor Efficiency Gains (reduced travel time)
Example Calculation:
- Current storage cost: $10/sq. ft.
- High-density storage increases capacity by 40%
- Annual savings: $10,000+ in avoided expansion costs
(For a detailed custom ROI analysis, consult a warehouse design expert.)
Installation & Best Practices for High-Density Double Deep Racking
1. Proper Floor & Load Planning
- Ensure floor strength supports double-deep loads.
- Use uniform pallet sizes for smooth operation.
2. Choosing the Right Forklifts
- Reach trucks (10–12 ft. aisles)
- Turret trucks (for very narrow aisles)
3. Safety Measures
- Column protectors to prevent forklift damage.
- Pallet backstops to avoid shifting.
4. Regular Maintenance
- Inspect uprights, beams, and forklifts routinely.
Future-Proofing Your Warehouse with High-Density Storage
As e-commerce demand grows, warehouses must adapt storage strategies. High-density double deep racking provides a scalable, space-efficient solution that can evolve with your business.
By integrating WMS (Warehouse Management Systems), businesses can further optimize inventory flow within high-density setups.
Conclusion: Should You Switch to High-Density Double Deep Racking?
High-density double deep racking is a powerful storage solution for warehouses needing higher density without sacrificing efficiency. While it requires specialized equipment and uniform loads, the space savings and cost benefits often outweigh the drawbacks.
Before making the switch, evaluate your SKU velocity, pallet consistency, and forklift capabilities. If your operation fits the criteria, high-density storage could be the key to unlocking 50% more storage capacity.
For a customized ROI assessment, consult a warehouse storage expert today.
Frequently Asked Questions (FAQs)
1. Can high-density double deep racking work with standard forklifts?
No, it requires narrow aisle or reach trucks due to the two-deep storage design.
2. What’s the maximum height for high-density double deep racking?
Most systems support up to 40 ft., but this depends on forklift reach capabilities.
3. Is high-density double deep racking suitable for cold storage?
Yes, but forklift batteries may require cold-weather adaptations.
4. How does high-density double deep racking compare to mobile shelving?
Mobile shelving offers higher density but slower access, while double deep balances space and speed.
5. Can I convert my existing selective racking to high-density double deep?
Yes, but it requires structural adjustments and new forklifts.
By following this expert guide, you’ll be equipped to decide if high-density double deep racking is the right warehouse optimization strategy for your business.