📐 "First 50 Enterprise Queries Get Custom 3D Warehouse Design" Plan
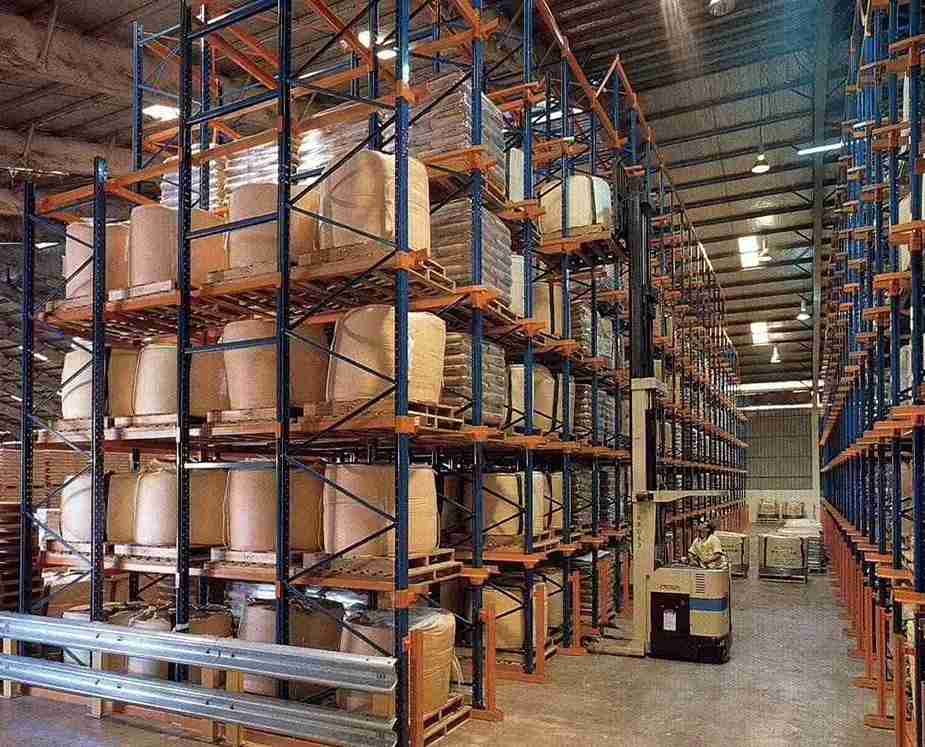
Introduction
In today’s competitive warehousing landscape, maximizing storage capacity without expanding facility footprints has become critical. Drive-in racking systems have emerged as one of the most efficient solutions for operations requiring high-density storage of homogeneous products. Unlike conventional selective pallet racking, drive-in racking systems allow forklifts to enter the storage structure directly, dramatically increasing pallet positions per square foot.
This definitive guide explores every aspect of drive-in racking systems, providing warehouse managers, logistics professionals, and storage system designers with actionable insights. The comprehensive analysis covers:
-
Operational mechanics of drive-in racking systems
-
Structural engineering considerations
-
Comparative advantages over alternative storage systems
-
Industry-specific applications demonstrating real-world effectiveness
-
Safety protocols and maintenance best practices
-
Cost-benefit analysis and return on investment calculations
With over 70% of cold storage facilities and bulk beverage distributors now utilizing drive-in racking systems, understanding this storage solution has become essential for competitive operations.
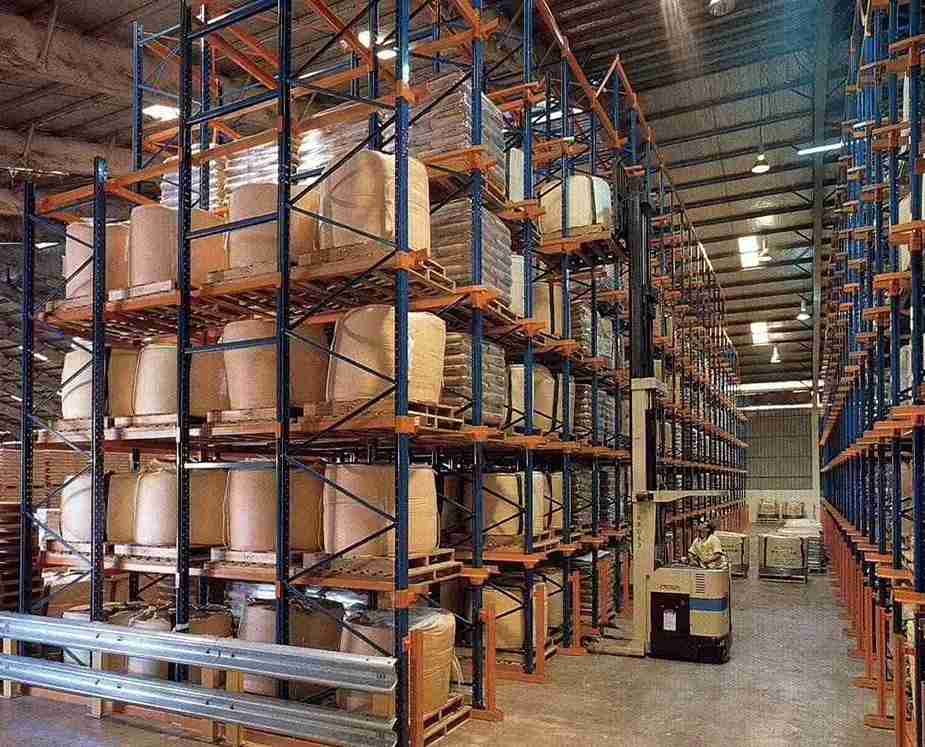
H1: The Engineering Behind Drive-In Racking Systems
H2: Structural Design Principles
Drive-in racking systems employ a unique structural configuration that differs fundamentally from traditional pallet racking. The system consists of:
-
Continuous rail channels replacing individual beam levels
-
Heavy-duty upright frames with reinforced base plates
-
Integrated guide rails for precise forklift navigation
-
Impact-resistant backstops preventing pallet over-extension
This engineered approach allows drive-in racking systems to support up to 50% more pallet positions than selective racking in the same floor space, making them ideal for operations with space constraints.
H2: Load Capacity and Configuration Variables
The performance characteristics of drive-in racking systems vary based on several configurable parameters:
Configuration Option | Typical Range | Performance Impact |
---|---|---|
System Depth | 4-12 pallet positions | Deeper = higher density but reduced accessibility |
Clearance Height | 20-45 feet | Requires specialized forklift equipment |
Beam Load Rating | 5,000-15,000 lbs | Determines product weight capacity |
Aisle Width | 96-144 inches | Varies by forklift turning radius |
Proper configuration of drive-in racking systems requires careful analysis of product dimensions, turnover rates, and material handling equipment capabilities.
H1: Operational Advantages of Drive-In Racking Systems
H2: Space Utilization Metrics
Comparative studies demonstrate that drive-in racking systems achieve:
-
85-90% floor space utilization vs. 60-65% for selective racking
-
3-5x more pallet positions in the same footprint
-
40% reduction in required aisle space
These metrics explain why drive-in racking systems dominate applications where real estate costs exceed $12/sq ft annually.
H2: Cost Efficiency Analysis
The economic benefits of drive-in racking systems become apparent when examining total cost of ownership:
Case Study: Regional Food Distribution Center
-
Facility Size: 150,000 sq ft
-
Prior System: Selective racking (32,000 pallet positions)
-
After Conversion: Drive-in racking systems (51,000 positions)
-
ROI Period: 2.3 years
-
Annual Savings: $380,000 in avoided expansion costs
This demonstrates how drive-in racking systems can defer or eliminate facility expansion requirements.
H1: Industry-Specific Implementations
H2: Cold Storage Applications
Temperature-controlled environments particularly benefit from drive-in racking systems due to:
-
Reduced energy loss from minimized air space
-
Higher storage density offsetting refrigeration costs
-
Compatibility with cold-optimized forklifts
Leading third-party logistics providers report 18-22% operational cost reductions after implementing drive-in racking systems in frozen storage operations.
H2: Automotive Parts Distribution
The automotive aftermarket sector utilizes drive-in racking systems for:
-
Bulk storage of slow-moving SKUs
-
Seasonal inventory buildup
-
Overflow storage during production surges
Toyota’s Kentucky parts distribution center achieved 37% better space utilization after installing drive-in racking systems for low-rotation components.
H1: Safety Engineering in Drive-In Racking Systems
H2: Collision Prevention Systems
Modern drive-in racking systems incorporate multiple safety features:
-
RFID-guided forklift navigation
-
Laser alignment systems
-
Impact monitoring sensors
-
Automatic slowdown zones
These technologies have reduced damage incidents by 72% in facilities using drive-in racking systems according to Material Handling Industry reports.
H2: Structural Integrity Monitoring
Best practices for maintaining drive-in racking systems include:
-
Quarterly laser alignment checks
-
Ultrasonic weld inspections
-
Load beam deflection measurements
-
Anchor bolt torque verification
Progressive operations now integrate IoT sensors into their drive-in racking systems for real-time structural health monitoring.
H1: Comparative Analysis with Alternative Systems
H2: Throughput Capacity Benchmarking
Recent benchmarking data reveals:
Storage System | Pallets/Hour | Density (Pallets/sq ft) |
---|---|---|
Selective Racking | 45-55 | 1.2-1.5 |
Drive-In Racking | 30-40 | 3.8-4.2 |
Push-Back Racking | 35-45 | 2.9-3.3 |
This demonstrates the trade-off between density and accessibility in drive-in racking systems.
H1: Future Trends in Drive-In Racking Technology
H2: Automation Integration
Emerging advancements include:
-
Automated guided vehicles (AGVs) designed specifically for drive-in racking systems
-
AI-powered slotting optimization algorithms
-
Predictive maintenance systems using vibration analysis
H2: Sustainable Materials
Manufacturers are developing:
-
High-strength recycled steel components
-
Energy-absorbing composite materials
-
Corrosion-resistant coatings for harsh environments
H1: Conclusion
Drive-in racking systems represent a sophisticated storage solution that continues evolving to meet modern logistics challenges. Their unparalleled space utilization makes them indispensable for bulk storage applications, particularly in cold storage, beverage distribution, and manufacturing sectors.
Operations considering drive-in racking systems should conduct thorough:
-
Product profile analysis
-
Throughput requirement studies
-
Total cost modeling
-
Safety assessments
When properly specified and maintained, drive-in racking systems deliver exceptional ROI while future-proofing warehouse operations against space constraints.
H1: Frequently Asked Questions (FAQs)
H2: What forklift specifications work best with drive-in racking systems?
Drive-in racking systems require:
-
96-144 inch aisle capability
-
Mast heights exceeding storage elevation
-
Precision guidance systems
-
5,000+ lb lift capacity
H2: How frequently should drive-in racking systems be inspected?
OSHA mandates annual inspections, but best practice for drive-in racking systems includes:
-
Quarterly structural assessments
-
Monthly visual checks
-
Post-impact examinations
H2: Can drive-in racking systems accommodate multiple SKUs?
While primarily designed for single-SKU storage, advanced drive-in racking systems can:
-
Segment lanes with dividers
-
Incorporate digital labeling
-
Utilize mixed-depth configurations
H2: What fire protection systems integrate with drive-in racking?
Modern drive-in racking systems support:
-
In-rack sprinkler systems
-
Smoke detection arrays
-
Thermal monitoring networks
H2: How does seismic activity affect drive-in racking systems?
Engineered drive-in racking systems in seismic zones require:
-
Base isolators
-
Cross-aisle bracing
-
Reduced height profiles
-
Dynamic load calculations