📐 "First 50 Enterprise Queries Get Custom 3D Warehouse Design" Plan
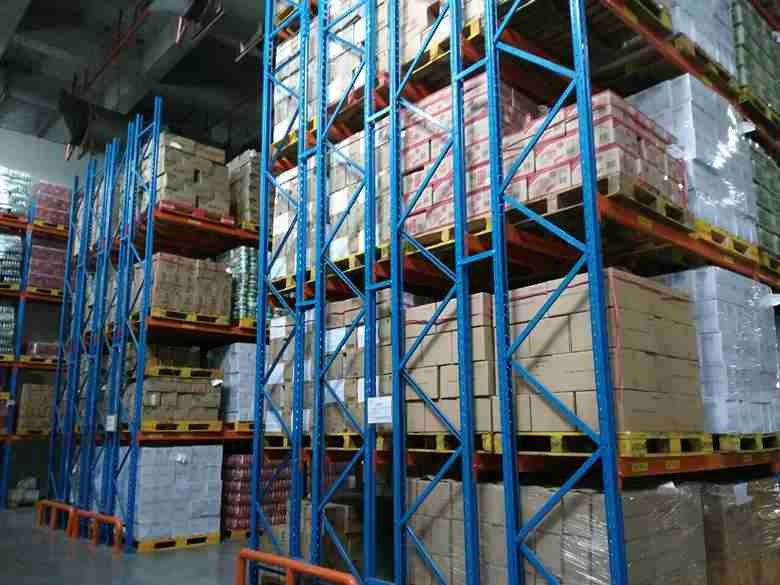
Introduction: Unlocking Warehouse Potential with Double Deep Racking
In an era where every square foot of warehouse space translates directly into cost savings or revenue potential, double deep racking emerges as a transformative storage solution. Unlike conventional single-deep systems, double deep racking effectively doubles storage capacity by utilizing two pallet depths—revolutionizing how businesses approach inventory management.
For warehouse managers, logistics coordinators, and operations directors, double deep racking isn’t just another shelving option—it’s a strategic investment that slashes real estate costs, enhances storage density, and optimizes workflow efficiency. But is it the right fit for every operation?
This in-depth guide explores:
✔ How double deep racking works—and why it outperforms traditional systems
✔ Real-world applications across industries (from food distribution to e-commerce)
✔ Cost vs. benefit analysis—when does double deep racking make financial sense?
✔ Critical safety considerations—avoiding costly accidents and product damage
✔ Head-to-head comparisons with drive-in, push-back, and selective racking
By the end, decision-makers will have a clear, actionable understanding of whether double deep racking aligns with their operational needs—and how to implement it for maximum ROI.
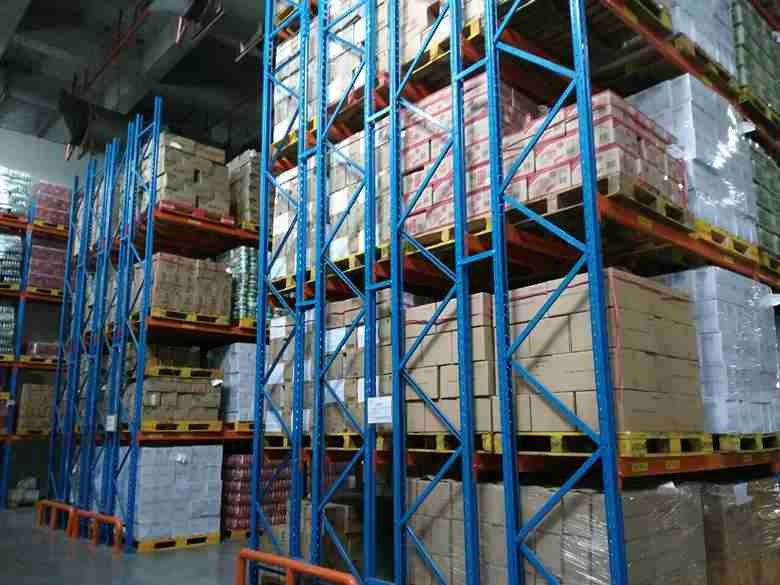
1. The Mechanics of Double Deep Racking: How It Transforms Storage Capacity
1.1 Structural Engineering Behind Double Deep Racking
At its core, double deep racking is a high-density storage system where pallets are stored two-deep rather than single-deep. This configuration requires:
-
Heavy-duty upright frames (typically 12–14 gauge steel)
-
Reinforced load beams designed for double-depth weight distribution
-
Optional wire mesh decking for added stability and fall protection
Unlike selective racking, where every pallet is immediately accessible, double deep racking positions two pallets back-to-back in each bay. This design increases storage by 40–60% compared to single-deep systems while maintaining relatively good selectivity.
1.2 The Forklift Factor: Specialized Equipment for Double Deep Racking
Standard forklifts cannot retrieve pallets from the second position—this is where specialized equipment becomes essential:
-
Double-deep reach trucks: Forklifts with extendable forks (up to 96″ reach)
-
Narrow-aisle (NA) forklifts: For operations with tight clearances (as little as 10–12 ft aisles)
-
Automated guided vehicles (AGVs): Emerging tech for fully automated retrieval
Pro Tip:
When budgeting for double deep racking, factor in the cost of compatible forklifts—this can significantly impact total ROI.
2. Why Leading Warehouses Are Switching to Double Deep Racking
2.1 Space Optimization: Store More Without Expanding
For warehouses facing sky-high real estate costs, double deep racking is a game-changer. By eliminating every other aisle (compared to selective racking), businesses can:
-
Increase pallet positions by 60–90% in the same footprint
-
Delay or avoid costly facility expansions
-
Reduce per-pallet storage costs by maximizing vertical and horizontal space
Case Study:
A Midwest beverage distributor increased storage capacity by 72% after switching to double deep racking, avoiding a $2M warehouse expansion.
2.2 Cost Efficiency: Lower Operational Expenses
While the upfront investment is higher than selective racking, double deep racking delivers long-term savings through:
-
Reduced facility costs (smaller footprint = lower rent/utilities)
-
Higher inventory turnover potential (ideal for FIFO/LIFO workflows)
-
Lower labor costs (fewer aisles = faster forklift travel times)
2.3 Ideal for Bulk Storage with Medium Selectivity
Double deep racking shines when storing:
-
High-volume SKUs (e.g., pallets of the same product)
-
Slow-to-moderate turnover inventory (not ideal for ultra-fast-moving goods)
-
Non-perishable items where immediate access isn’t critical
3. Limitations of Double Deep Racking: When to Consider Alternatives
3.1 Accessibility Trade-Offs
The primary drawback of double deep racking is reduced selectivity:
-
Must move the front pallet to access the rear pallet
-
Not ideal for high-mix, low-volume (HMLV) inventory
-
Slower picking times compared to selective racking
3.2 Higher Upfront Costs
-
Specialized forklifts ($30K–$60K per unit)
-
Stronger racking components (heavier beams/columns)
3.3 Not Ideal for Perishables or High-Turnover SKUs
Industries like cold storage or pharmaceuticals may prefer selective racking for instant access.
4. Industry-Specific Applications of Double Deep Racking
4.1 Food & Beverage: Perfect for Bulk Dry Goods
✔ Canned foods, bottled beverages, packaged snacks
✔ FIFO-compatible with proper rotation
4.2 Retail & E-Commerce: Backstock Optimization
✔ Seasonal overstock storage
✔ High-volume SKUs with predictable demand
4.3 Automotive & Manufacturing: Raw Material Storage
✔ Tires, metal coils, bulk components
✔ LIFO systems where last-stored items are used first
5. Double Deep Racking vs. Competing Systems
5.1 Double Deep vs. Selective Racking
Factor | Double Deep Racking | Selective Racking |
---|---|---|
Storage Density | 60–90% higher | Standard |
Accessibility | Medium (2-deep) | Instant (1-deep) |
Best For | Bulk storage | High-mix inventory |
5.2 Double Deep vs. Drive-In Racking
-
Drive-in racking allows deeper storage (6+ pallets deep) but zero selectivity
-
Double deep racking offers better access while still improving density
6. Implementing Double Deep Racking: Safety & Best Practices
6.1 Warehouse Layout Optimization
-
Aisle width: 10–12 ft for reach trucks
-
Load balancing: Heavier pallets at the base
6.2 Forklift Operator Training
-
Specialized training for double-deep reach trucks
-
Collision avoidance systems (laser guidance, sensors)
7. Cost Breakdown & ROI Calculation
7.1 Upfront Investment
-
Racking system: $50–$100 per pallet position
-
Forklifts: $30K–$60K each
7.2 Payback Period
Most operations see ROI within 2–3 years through:
✔ Reduced facility costs
✔ Higher storage utilization
8. The Future of Double Deep Racking
✔ Automation integration (AGVs, robotic retrieval)
✔ AI-driven slotting optimization
Final Verdict: Is Double Deep Racking Right for Your Operation?
For warehouses with:
✅ High-volume, low-SKU-variety inventory
✅ Space constraints driving up costs
✅ Moderate product turnover
Double deep racking delivers unmatched space savings and operational efficiency. However, businesses needing instant access to every pallet should consider selective racking instead.
Next Steps:
-
Conduct a storage density analysis—how many additional pallets could you store?
-
Evaluate forklift compatibility—do you need new equipment?
-
Consult a racking specialist—get a custom layout designed for your needs.
FAQs: Expert Answers on Double Deep Racking
1. Can I retrofit my existing selective racking into double deep?
Yes, but it requires additional upright frames, beams, and a compatible forklift.
2. What’s the maximum weight capacity per bay?
Typically 20,000–30,000 lbs, but consult an engineer for exact specs.
3. How much aisle space is needed for double deep racking?
10–12 feet, depending on forklift type.
4. Is double deep racking suitable for cold storage?
Yes, but ensure forklifts are cold-rated.
5. What’s the lifespan of a double deep racking system?
20+ years with proper maintenance.