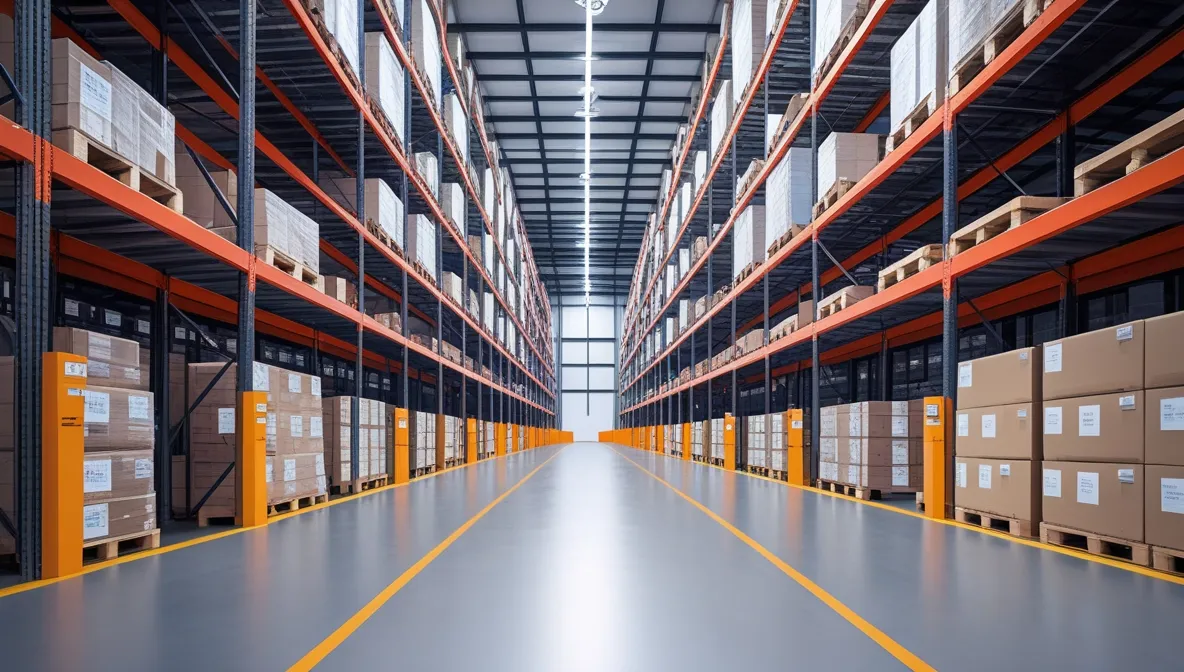
Introduction
In today’s fast-paced industrial world, Factory Storage Layout Optimization is crucial for maintaining efficiency, reducing costs, and maximizing space utilization. A poorly designed warehouse layout leads to wasted space, inefficient workflows, and safety hazards, all of which impact the bottom line. Did you know that businesses implementing optimized storage layouts see a 30% increase in operational efficiency?
This guide explores how Factory Storage Layout Optimization can transform your facility, covering key principles, real-life case studies, and actionable strategies to improve warehouse efficiency. Whether you want to enhance Factory Storage Optimization ROI, streamline Lean Warehouse Layout, or integrate vertical warehousing solutions, this article will provide insights backed by industry best practices.
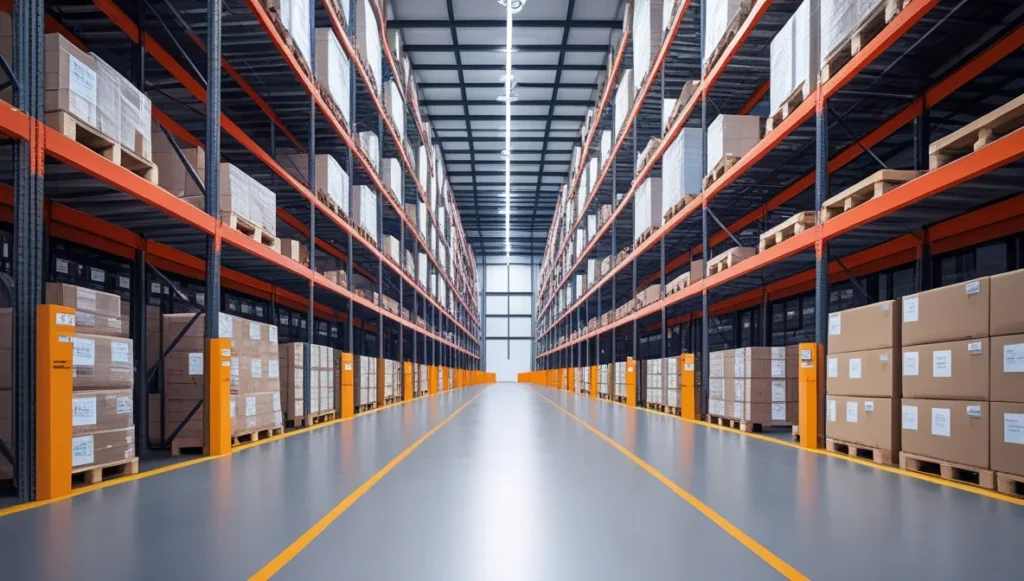
1. Why Factory Storage Layout Optimization is Essential
1.1 The Cost of Poor Storage Planning
A disorganized storage system can lead to:
- Lost productivity: Employees waste time searching for inventory.
- Increased safety risks: Poorly arranged materials increase accident rates.
- Excessive inventory costs: Overstocking or misplacing inventory leads to financial losses.
- Limited scalability: Poor layouts restrict business growth and efficiency.
1.2 Benefits of an Optimized Factory Storage Layout
- Maximizes space utilization: Reduces wasted aisle space and enhances vertical storage.
- Improves workflow efficiency: Minimizes travel time for workers and boosts productivity.
- Reduces operational costs: Eliminates excess inventory and streamlines storage management.
- Enhances warehouse safety: Implements compliance standards and clear organization.
According to a study by the Warehouse Optimization Institute, companies that invest in Factory Storage Layout Optimization see up to a 40% reduction in wasted space and a 25% increase in storage efficiency.
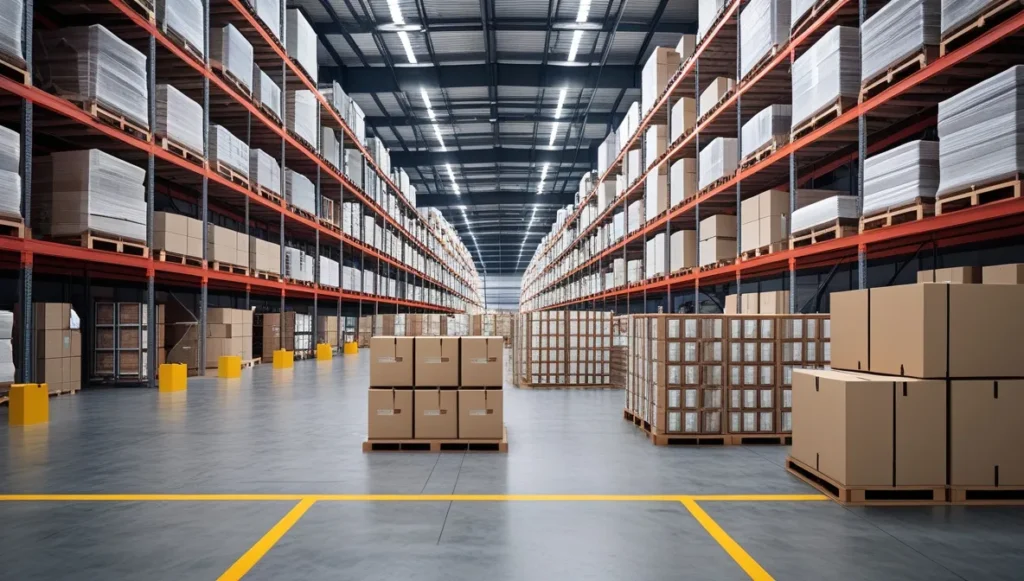
2. Core Strategies for Factory Storage Layout Optimization
2.1 Space Utilization: Maximizing Every Inch
Key Techniques:
- Vertical storage solutions: Implement mezzanines and multi-tier shelving.
- Compact storage systems: Use mobile shelving and high-density racks.
- Optimized aisle spacing: Implement narrow aisle racking for better space efficiency.
2.2 Smart Inventory Management for Optimization
Applying inventory categorization techniques can improve warehouse efficiency:
- FIFO (First In, First Out): Ensures older stock is used first.
- ABC Analysis: Prioritizes high-value items for easy access.
- Barcode and RFID tracking: Improves inventory accuracy and retrieval speed.
2.3 Lean Warehouse Layout: Streamlining Workflow
A Lean Warehouse Layout reduces travel time and optimizes material flow by:
- Placing high-demand items in accessible zones.
- Organizing sections based on workflow efficiency.
- Using conveyor systems and automation for high-speed order fulfillment.
2.4 Safety and Compliance Considerations
- Install guardrails and barriers to prevent accidents.
- Maintain clearly marked pathways to ensure smooth operations.
- Implement OSHA-approved weight distribution policies to prevent shelf collapses.
3. Case Studies: Real-Life Applications of Factory Storage Layout Optimization
3.1 Case Study: Automotive Manufacturing Facility
An automotive parts supplier was struggling with inventory mismanagement and space congestion. By implementing a Factory Storage Layout Optimization strategy:
- Installed vertical storage racks, increasing storage capacity by 35%.
- Introduced an RFID tracking system, reducing order retrieval time by 50%.
- Created a Lean Warehouse Layout, cutting worker travel time by 20%.
Result: The company saved $500,000 annually in operational costs and significantly boosted workflow efficiency.
3.2 Case Study: E-commerce Distribution Center
A major e-commerce retailer needed better space efficiency due to rapid business growth. They optimized their factory storage layout by:
- Implementing AS/RS (Automated Storage and Retrieval Systems).
- Utilizing ABC Analysis to reorganize inventory by demand.
- Installing mobile shelving systems, reducing required storage space by 40%.
Result: The facility increased storage efficiency by 30% and reduced labor costs by 25%.
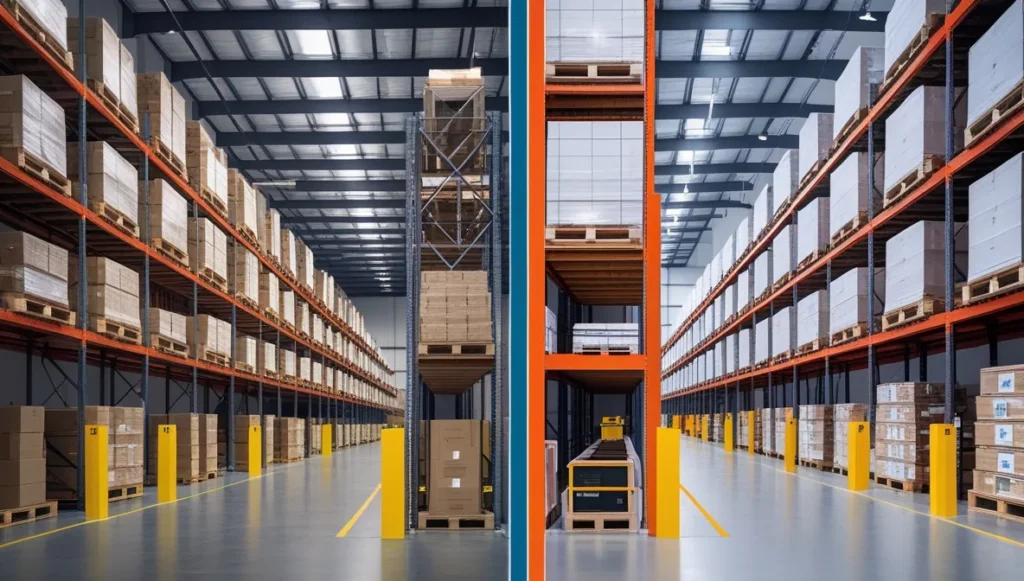
4. Best Storage Solutions for Factory Optimization
4.1 Pallet Racking Systems
Ideal for bulk storage:
- Selective Pallet Racks: Provides easy access to all inventory.
- Push-Back Racks: Uses gravity to move inventory forward.
- Drive-In Racks: Maximizes space efficiency by reducing aisle needs.
4.2 Mobile Shelving Units
- Increases storage capacity by up to 50%.
- Ideal for small factories needing dynamic storage solutions.
4.3 Automated Storage & Retrieval Systems (AS/RS)
- Reduces labor costs and increases inventory accuracy.
- Speeds up order fulfillment by 60%.
4.4 Cantilever Racks
- Designed for long, bulky materials like pipes and lumber.
- Provides easy, open-access storage for oversized items.
4.5 Mezzanine Storage Systems
- Creates additional storage without facility expansion.
- Ideal for non-heavy stock storage.
5. Implementing a Factory Storage Optimization Plan
Step 1: Assess Storage Needs
Evaluate current warehouse space usage and identify inefficiencies.
Step 2: Plan an Efficient Layout
Use CAD software to design a new storage plan.
Step 3: Choose the Right Storage System
Select solutions based on Factory Storage Optimization ROI.
Step 4: Implement Smart Inventory Management
Install barcode/RFID tracking for efficient stock control.
Step 5: Train Employees
Ensure staff is familiar with the new Lean Warehouse Layout.
Step 6: Monitor & Improve
Regularly audit storage performance and adjust as needed.
Conclusion
Investing in Factory Storage Layout Optimization enhances productivity, minimizes costs, and maximizes space utilization. By implementing best practices such as vertical storage, ABC Analysis, and automated retrieval systems, companies can significantly improve warehouse efficiency.
Download Our Free Storage Audit Checklist to start optimizing your warehouse today!
Frequently Asked Questions (FAQ) on Factory Storage Layout Optimization
Q1: What are the first steps in optimizing a factory storage layout?
A1: Start by evaluating your current warehouse space and identifying inefficiencies. Use a Storage Audit Checklist (Download Here) to analyze:
-
- Storage density: Identify underutilized areas.
- Inventory accessibility: Optimize pick paths and reduce travel time.
- Safety & compliance: Ensure OSHA standards and weight distribution regulations are met.
🔗 Related Resource: [5S Methodology Guide: Organizing for Efficiency]
📊 Infographic Available – “Factory Storage Optimization Roadmap”
Q2: How does vertical storage improve efficiency?
A2: Implementing vertical racking systems can increase storage capacity by up to 40% without expanding your facility. Solutions include:
-
- Mezzanine storage systems for non-heavy stock.
- Automated Storage & Retrieval Systems (AS/RS) for high-speed order processing.
- Cantilever racks for long and bulky materials.
📽️ Video Demo Available – “How AS/RS Transforms Warehouse Storage”
Q3: What is the ROI of Factory Storage Layout Optimization?
A3: Companies investing in Factory Storage Optimization ROI typically experience:
✅ 30% increase in productivity due to better workflow.
✅ 25% reduction in storage costs from improved space utilization.
✅ 50% faster order processing with automation integration.
🔗 Case Study: [Automotive Supplier Saves $500K with Layout Optimization]
📊 Infographic Available – “Cost Savings Breakdown of Storage Optimization”
Q4: How does Lean Warehouse Layout contribute to efficiency?
A4: A Lean Warehouse Layout optimizes workflow by:
-
- Placing high-demand inventory in accessible zones.
- Reducing unnecessary travel paths with strategic item placement.
- Implementing conveyor systems and robotics for automation.
📽️ Video Available – “Lean Warehousing: How to Reduce Waste & Maximize Efficiency”
🔗 Downloadable Resource: [Warehouse Layout Planning Checklist]
Q5: What storage systems are best for my facility size?
A5: Your choice depends on warehouse size and operational needs:
-
- Small facilities: Mobile shelving & mezzanine systems.
- Medium-sized warehouses: Selective pallet racking & FIFO-based storage.
- Large-scale operations: AS/RS & automated vertical storage.
📊 Infographic Available – “Choosing the Right Storage System for Your Facility”
🔗 Read More: [Best Industrial Storage Systems for Different Warehouse Sizes]